|
|
1) |
If you have an LCD display or MD-HMI, then
connect the 14-way LCD cable to the LCD port. But for now DON"T CONNECT the
expansion board or the 10-way ribbon cable from the MD-HMI to the PLC's expansion
port. We want to be able to isolate the problem (if any) to the PLC itself and so do
not want the expansion board to affect the result. Next, connect 24VDC power supply to
to the T100MD888+ PLC. Make sure that the power supply polarity is correct before turning
on power. Turn on the power supply. The green power LED on the PLC should light up. Use a
voltmeter to verify that valid DC voltage is available at the power supply screw terminal.
Note that T100MD888+ may also be powered by 12VDC power supply, but you should short
jumper J1 (which is next to power supply LED) using the provided jumper block when
connecting 12V to the PLC.
If the T100MD888+ CPU is alive and the output circuit are working, then you should see
the three status LEDs (green RTCError, red Pause, red RunError) light up for between 1 to
3 seconds (depending on the length of program residing in the PLC) and then the Pause and
RunError LED should go off. RTCError LED will remain lighted if there is no MX-RTC
installed. This indicates that the CPU has successfully loaded the program from the
EEPROM and the program will run immediately.
If the status LED did not light up, or they do not turn off after lighting up, and you
have verified that the power supply voltage is correct, then there is some serious problem
with the PLC. You should contact support@tri-plc.com
and request for an RMA # and RMA procedure to send the PLC to our service center for
service and repair. |
2) |
If smoke or burning smell appears after the power supply is
turned ON, then turn it OFF immediately. Most likely it is either the power supply has
been connected in reverse polarity, or the output driver ULN2803A or ULN2003A is
damaged due to overload. Check for visual clue. Remove ULN2803A and ULN2003A output driver
from its socket if you are not sure, then apply power to the PLC again. If there is no
more smoke then it is most likely a shorted ULN2803A or ULN2003A. You can purchase this
part number easily from many electronic component supplier such as Digikey or Jameco or
contact support@tri-plc.com to purchase the part. If
the PLC status LED lights up and goes off as described above, and the power supply is
steady, you may like to check the power supply current to the PLC using a mA meter by
connecting the meter in series between the +24V power supply and the PLC's positive power
terminal. If the supply current exceeds 150mA while all outputs are OFF then there is
likely to be some damaged components on the PLC. You should contact support@tri-plc.com and request for an RMA # and RMA
procedure to send the PLC to our service center for service and repair.
|
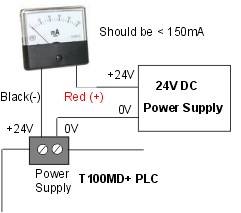
|
|
3) |
Connect the male end of the DB9 cable to T100MD888+ PLC's
RS232 port (COMM1), and the female end of the DB9 cable to the PC's serial port. Run
TLServer version 2.x or 3.x. Click "Serial Port Setup" on TLServer front panel.
Check to ensure that the correct COM port is selected and that the baud rate is 38,400, 8
data bits, 1 stop bit and None for parity, 'Time out' is 500ms. If you need to make any
changes, click on the "Close Port" button first. At the "Command
String" text field, enter "IR*" and
press <Enter>". If the PLC returns a response string "IRnn*" (where nn is a hexadecimal number
between 00 and FF, the default is "IR01*") then
you have successfully established communication with the PLC. If there is no response from
PLC, click on the "Close Port" button, and select another COM port from the
"Port Name" choice box and try again.
Note: If you receive a response string "IR*" (without the ID) then the COM port is not a valid COM
port (most likely it is a modem port) and what you receive is merely an echo of the
command you sent to the COM port. It is not a response from the PLC
|
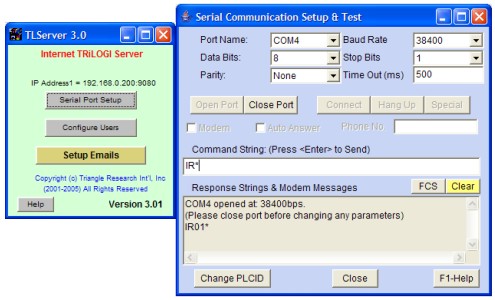 |
|
4) |
If you receive no response from the PLC, then
it could be one of the following reasons:
- The PLC program has altered the COMM1 port setting or the PLC program is writing out of
the COMM1 port and therefore interfering with the host link command that TLServer
try to send to it.
- The PLC's COMM1 port is bad.
- The PC's COM port is bad. You can test whether the PC's COM port is working by testing
the COM port with other devices, or change a PC and try the same test mentioned above.
Quite frequently the problem is due to (a) which happens that the previous program
loaded into the PLC has somehow altered the COMM1 port setting or disable it altogether
when the program run. You can recover the PLC by turning ON DIP switch #4 to ON, then
power cycle the PLC. You will see that the red "Pause" status LED will remain
lit after the CPU has loaded its program from the EEPROM. DIP Switch #4 halts the
CPU and prevent it from executing any PLC program so that the COMM1 port settings will not
be changed by the program.
When a T100MD+ PLC is power-ON RESET with DIP switch #4 on, the CPU set the COMM1 port
default baud rate to 9600 bps, 8 data bits, 1 stop bit and no parity. Hence you must click
on the "Close Port" button on the "Serial Communication Setup &
Test" window, change the baud rate to 9600 bps, and then re-try the "IR*" command to see if you can get a valid "IRnn*" response from the PLC. If you do get a
valid response this time, then please use TRiLOGI to transfer a blank program to the PLC
to overwrite the offending program. You would have recovered the PLC by now and you can
then turn OFF DIP switch #4, power-cycle the PLC and then change the TLServer serial port
back to 38,400 bps. You should now be able to send the "IR*" command and get a proper "IRnn*" response from the PLC.
If the above procedure is unsuccessful, then the PLC's COMM1 port may be damaged. You
may want to contact info@tri-plc.com to request for
an RMA if you prefer not to deal with desoldering/soldering of transistors. Otherwise, the
two active components that control the T100MD+ PLC's COMM1 port are a PN2222 and a 2N4403
which are located just below the 74HC595 LCD driver IC. If you replace these two
transistors the COMM1 port should be OK. |
5) |
If TLServer communication with the PLC is OK,
then you can now use TRiLOGI software to transfer the program "mdtest.pc5" (a
copy is available at: http://www.tri-plc.com/selftest/plctestprograms.zip ) to the
T100MD888+ PLC. The LEDs for output 1 to 6 should be blinking once every second after the
program has been transferred to the PLC. The LEDs for output #7 and #8 should be changing
their intensity from dimmest to the brightest repeatedly. This indicates that the PWM
outputs are functioning properly. |
6) |
Digital I/O Test Connect
one end of a wire to the 0V terminal of the power supply and use the other end of
the wire as a probe to touch the screw terminal of input #1 to #8. The corresponding
output #1 to #8 will be turned ON immediately in response to input #1 to #8. If all
outputs respond properly to the activation of their corresponding inputs, then the PLC has
passed the digital I/O test.
If an output LED does not light up when it is supposed to, then it could be a bad LED
or a damaged output driver IC: ULN2003A, ULN2803A or the IRL530 (3 pin TO220 package)
MOSFET. You can use a multi-meter's diode test range to probe on the two LED legs and see
if it lights up. If the LED lights up when probed by meter, but does not light up when the
output is supposed to be turned ON, then most likely it is the damage to the output
driver. The following ICs control the outputs:
Output 1-4 : UD1 (ULN2803A) & UO1 (74HC595); Output 5 & 6: UD2 (ULN2003A).
Output 7: QU1 (IRL530); Output 8: QU2 (IRL530);
Note: UO1 also controls the 3 status LEDs.
LCD port Test
If a good LCD display was connected to the
PLC, you should observe the message "Input 1-16 OK" on the second line of the
LCD display. If a connected LCD shows nothing, it could be a bad LCD driver U5 (74HC595)
that needs to be replaced. You may also want to turn the LCD constrast preset
potentiometer (just below the RS485 terminal) to fully anti-clockwise (maximum constrast)
in case it has be adjusted by someone else to see if the character shows up on the LCD
display. The LCD display itself also could be damaged if you have previously
plugged/unplugged the LCD connector without turning off the power to the PLC first. If the
LCD display is damaged it is not repairable and need to be replaced with a new purchase. |

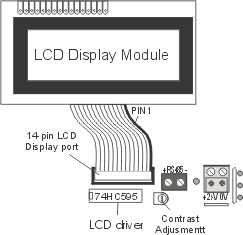
|
|
7) |
Expansion Port Test If
you are using the MD-HMI, then you'll also need to test the PLC's expansion port. First,
TURN OFF POWER to the PLC, then connect the the 10 way IDC cable from the MD-HMI to the
PLC's expansion port. Turn ON power to the PLC and press the key 0 to 7 on the MD-HMI. The
8 signal LEDs on the MD-HMI should light up one at a time when the key is pressed. This
indicates that the expansion port on the T100MD-888+ PLC is functioning properly.
If you are using an Expansion board such as EXP1616R or EXP4040, then you can also use
it to test the PLC's expansion port. First, TURN OFF POWER to the PLC, then connect the
expansion board IDC connector to the PLC's expansion port. Turn ON power to the PLC and
turn ON and OFF each digital input on the expansion board. The corresponding digital
output should be turned ON and OFF immediately (i.e. input #17 controls output #17, input
#24 controls output #24, and so on). This indicates that the expansion port on the
T100MD-888+ PLC is functioning properly. |
8) |
Analog I/O Test With
the power to the PLC turned ON, use an accurate voltmeter to measure the voltage at the
AVcc solder pad (which is located just above the DB15 analog I/O connector on the PLC)
with respect to 0V of the PLC power supply. You should get a 5.00V reading. Otherwise you
can adjust the "Adj" preset pot (to the right of the AVcc sold pad) on the PLC
to calibrate the PLC's analog reference voltage until you obtain a 5.000V reading.
Solder a wire to the D/A#1 or D/A #2 pin on the DB15 connector (pin 2 & pin 1
respectively). The "mdtest.pc5" program you transferred to the PLC in the
digital I/O test would have set the analog output #1 and #2 to 2048 and 4000,
respectively. If you measure the voltage using a voltmeter, D/A #1 would record a reading
of 2.50V and D/A #2 would record a reading of 4.88V.
The "mdtest.pc5" program also reads the value of analog inputs 1-6
continuously. So if you use the wire connected to D/A #1 and touch analog inputs #1 to #6,
you will be able to observe the analog input reading of approximately 2048 via the online
monitoring -> View Variable screen. And if you use the wire connected to D/A #2 and
touch analog input 1-6, you will observe the analog input reading of approximately 4000 on
the online monitoring. Note that analog inputs that are not connected to any voltage
(i.e. floating) will not record zero reading, instead they tend to float around the
reading of the adjacent pins and hence the readings are indeterminate for those
disconnected analog inputs.
If A/D #1 to #6 and D/A #1 and #2 output the correct voltages, then the PLC has passed
the analog I/O test |
 |
|
9) |
RS485 Test To test the
RS485 port, you'll need to connect the PC''s RS232 port to the DB9 side of the Auto485
adapter and also connect a 9 to 24V power supply to Auo485. Next, connect RS485 (+)
terminal on the Auto485 to the PLC's RS485 (+) terminal and do the same for the RS485 (-)
terminals.
Next, use the TRiLOGI program to perform online monitoring of the PLC exactly the same
way when the PC is connected to the PLC's RS232 port. If successful you will also see the
green and red Tx and Rx LEDs on the Auto485 blinking rapidly as the PC communicates with
the PLC via RS485.
If the RS485 failed to work, then most likely it is the 8 pin RS485 driver
"75HVD3082" that is damaged. Since this is a socketed IC you should be able to
find a replacement from electronic component supplier such as Digikey or contact support@tri-plc.com to purchase the IC. (Note: an
easier to find substitute part number is SN75176).
|
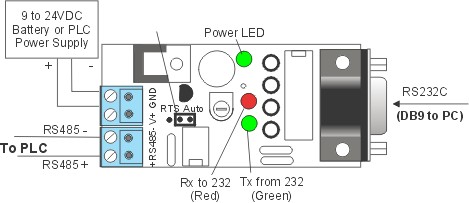 |
If the T100MD888+ PLC passed all the above functional tests, then it
essentially has no problem and may be put to production use. |